Lean Six Sigma Black Belt Training and Certification equips you with “Advanced Practitioner Level” perspectives and skills in process variability reduction (DMAIC), process waste reduction (LEAN) and a comprehensive toolkit to plan and lead change in your organization.
This course builds upon your Green Belt knowledge to expand your Lean Six Sigma expertise, strengthen your knowledge and skill sets, and gives you the confidence you need to take that next step as a continuous improvement professional and return back to your organization with a greater level of analytical, project implementation and change leadership skills.
You walk away with the learning and the know-how. This means not just focus on the “what” to do but the “how” to do it, with greater emphasis on typical project barriers and “hints” and “tips” on “how” to overcome using case studies and compelling best practices as part of the learning experience.
Come with a change initiative
What are change initiatives?
Change initiatives are usually plans and actions aiming at implementing a process transformation in an organization that could result in a change of the culture, communication, human resource, logistics, and etc. Change initiatives come from all geographies, industries and career levels, so it’s hard to generalise.
Common examples of challenges
- Creating a company-wide culture of customer focus or digitalizing a product or service
- Motivating employees to accept changes in a continuously changing business environment
- Adopting a new organizational solution and making sure it’s fully implemented
- Setting up a new system in an overseas subsidiary – with a lot of push-back from local employees
- Facing the changes in employment/process/system due to taking over new markets or companies or being acquired by others.
Why are they important in this programme?
Having a change initiative(s) allows participants to contribute their unique experiences, personalise the tools to their own situation and make an impact back at the workplace. By the end, they have a clear set of priorities and are ready to create an action plan that can be used immediately upon their return to work.
It is not necessary but recommended that applicants have at least one change initiative, which allows them to adopt a learn by doing approach to apply learning outcomes to a real world scenario(s).
How you benefit:
- Sustain actionable knowledge. Harness information you already have into a solid understanding of how to build sustainable processes and structures to enhance your organization’s capability
- More competent as a manager. Become a more competent and confident manager with new insights, knowledge and skills.
- Elevate key skills in change leadership, analyzing data and decision making to take on greater responsibility to pinpoint and manage performance shortfalls
- Insights on where to focus attention to influence change in your organization and how to identify, scope and charter continuous improvement projects
- Master the skills you need to combine statistical and quantitative methods with the interpersonal skills required to influence, inform and drive change
- Develop coaching skills to guide team members and advise management during Lean Six Sigma implementation
- Action Learning Project to apply the learning in your personal or your organization’s context
Participant Profile:
Black Belt Training and Certification is designed for Certified Green Belt’s from a wide variety of manufacturing, service and transactional organizations either currently involved with, or who aspire to, or have recently gained continuous improvement responsibilities;
- Seeking to develop in-depth knowledge and analytical skills in process variability reduction (DMAIC) and process waste reduction (Lean)
- Who want to strengthen their ability to lead change and enhance their organization’s continuous improvement capability
- Participants coming in groups/teams to collaborate on an Action Learning project tailored to their organization’s context
Course Pre-requisites
Lean Six Sigma Green Belt Certificate either with Game Change or another bonafide training provider
(evidence required prior to course start).
Exam and Certification
Exam: 50 Questions
Duration: 70 min.
Pass Mark: 70%
Achieve 70% pass mark in the Black Belt multiple choice final exam
“Develop the competencies to build and align an effective change team”. Every company’s needs, culture, areas of focus and strategy are different. Therefore sometimes, simply putting people on a course isn’t enough to make the difference.
Just as your needs are unique, your training solution needs to be unique too if it is to truly make the difference and bring about the behavioural change you seek – which ultimately gives you a competitive advantage and more importantly, a return on your investment.
One of the biggest challenges of learning and applying continuous improvement is sustaining the momentum needed to achieve results. Designed around a series of brief doing and learning activities, Group Training provides direct and on-going engagement with our qualified Master Black Belt experts who bring substantial business and organizational experience working in both traditional ways, one to one, face to face or remotely.
Action Learning Project
Action Learning Projects (ALPs) are guided ‘real-world assignments’ and a core element of Game Change Group Training, designed to increase business impact, and to enable you to take newly acquired skills and apply them within the context of your actual job and organization. Allowing you to test ideas in a risk-free environment, then devise a realistic strategy plan that can be executed once you return to work.
Working with our Master Black Belt coach, you will design an ALP that is right for your organization and your personal learning objectives.
There are three phases to the ALP process:
- First, you will agree on the scope of your ALP with the MBB coach, to make sure it aligns with the learning objectives of the programme and culminates in a concrete goal.
- Second, in each of the 15 content weeks, you will work as a team to apply the tools and concepts learned during that week to your ALP.
- Third, at the end of the content weeks, you will synthesize your learning and develop concrete strategic recommendations for your organization, and submit them for team review. In the final week of the programme, the team review will take place and this will be facilitated by a Game Change Master Black Belt. During this team review participants will review the submissions and provide peer feedback. The final ALP and peer review process normally takes place between 10-14 days after the programme content finishes.
Game Change’s unique approach to Group Training can be tailored to include:
On-site Project Coaching: Project-focused discussion and one-on-one review sessions with a project leader or team.
Virtual Coaching: Typically 1-3 hour sessions with a Master Black Belt connected to participants via Zoom.
Project Toll-gate Reviews: Arranged around the DMAIC problem solving roadmap, facilitated review and assessment of key deliverables and application of Lean Six Sigma techniques during project implementation.
Facilitated Workshops: Led by a dedicated trainer and coach who can focus on your individual needs and help broaden understanding of key topics and guide you to achieve your learning objectives and leave you with specific takeaways and immediate next steps.
This course can be tailored to include as few as a single on-site session, or may be done completely virtually. The timing and content for the coaching sessions are agreed in advance to provide maximum impact/benefit to the participants and their projects.
You choose:
- The delivery style – classroom, virtual, eLearning, or a combination through blended learning.
- Choice of format and duration – to allow for an Action Learning Project (ALP) to be completed alongside the learning.
- The support needed – one-to-one coaching, group coaching and eLearning access duration.
- Additional case studies and subjects to include – pick out the additional topics or subjects that you want to learn.
- Timing – number of days at a time, start time, finish time, weekends, evenings, day shift or night shift.
- Certification – real projects, case studies or examinations with no projects.
- Projects – Develop new or use industry, company specific case studies.
- Feedback – access to our systems, monthly reports and discussions with trainers.
- Customized and branded courseware also translated in several languages.
- Guest speakers and benchmarking site visits built into training sessions.
Curriculum and Course Format
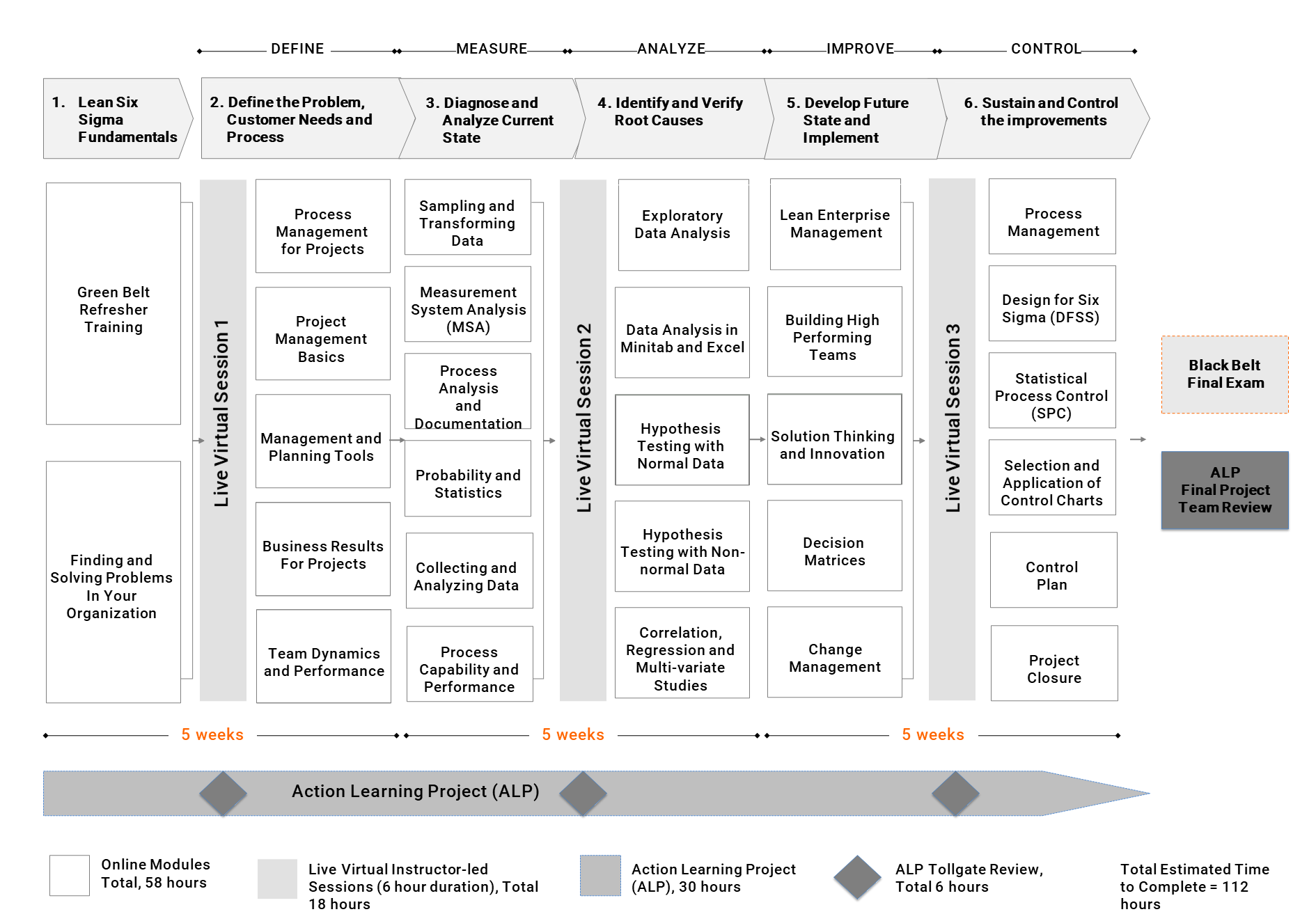
1.0 INTRODUCTION
4 Hours
Understand how lean and six sigma tools are applied to improve all types of processes in all types of enterprises: manufacturing, service, transactional, product and process design, innovation, etc.
Recognize key drivers for business (profit, market share, customer satisfaction, efficiency, product differentiation) and how key metrics and scorecards are developed and impact the entire organization.
1.1 Green Belt Refresher Training
1.2 Finding and Solving Problems in your Organisation
2.0 DEFINE
6 Hours
Define the scope and goals of the improvement project in terms of customer and/or business requirements, the process that delivers these requirements and stakeholder needs
2.2.1 |
Process elements |
2.2.2 |
Owners and stakeholders |
2.2.3 |
Identify customers |
2.3.1 | Collect customer data |
2.3.2 | Analyze customer data |
2.3.3 | Translate customer requirements |
2.4.1 | Building a Business Case & Project Charter |
2.4.2 | Project scope |
2.4.3 | Project metrics |
2.4.4 | Project planning tools |
2.4.5 | Project documentation |
2.4.6 | Project risk analysis |
2.4.7 | Project closure |
2.6.1 | Failure mode and effects analysis (FMEA) |
2.7.1 | Team stages and dynamics |
2.7.2 | Six sigma and other team roles and responsibilities |
2.7.3 | Team tools |
2.7.4 | Communication |
3.0 MEASURE
14 Hours
Calculate and interpret measures of dispersion and central tendency and construct and interpret frequency distributions.
Define and apply the concepts related to sampling (e.g., representative selection, homogeneity, bias, etc.) and select and use appropriate sampling methods (e.g., random sampling, stratified sampling, systematic sampling, etc.) that ensure the integrity of data. data.
Use various analytical methods (e.g., repeatability and reproducibility (R&R), correlation, bias, linearity, precision to tolerance, percent agreement, etc.) to analyze and interpret measurement system capability for variable and attribute measurement systems. Map the process and measure, understand and baseline the current process performance and capability through a set of relevant and robust measures.
Calculate process performance metrics such as defects per unit (DPU), rolled throughput yield (RTY), cost of poor quality (COPQ), defects per million opportunities (DPMO) sigma levels and process capability indices.
3.2.1 | Normality (Central Limit Theorem, P-values, Transforming Data) |
3.2.2 | Sampling Methods (Random and Process Sampling, Determining Sample Sizes, Selecting Samples) |
3.2.3 | EWMA Chart |
3.3.1 | Precision & Accuracy |
3.3.2 | Bias, Linearity & Stability |
3.3.3 | Gauge Repeatability & Reproducibility |
3.3.4 | Variable MSA |
3.4.1 | Process modeling |
3.4.2 | Process inputs and outputs |
3.5.1 | Drawing valid statistical conclusions |
3.5.2 | Central limit theorem and sampling distribution of the mean |
3.5.3 | Basic probability concepts |
3.6.1 | Types of data and measurement scales |
3.6.2 | Data collection methods |
3.6.3 | Techniques for assuring data accuracy and integrity |
3.6.4 | Descriptive statistics |
3.6.5 | Graphical methods |
3.6.6 | Probability distributions |
3.6.7 | Measurement System Capability |
distributions
3.6.7 Measurement System Capability
3.7.1 | Process capability studies |
3.7.2 | Process performance vs. specification |
3.7.3 | Process capability indices |
3.7.4 | Process performance indices |
3.7.5 | Short-term vs. long-term capability |
3.7.6 | Process capability for attributes data |
4.0 ANALYZE
10 Hours
Drawing valid statistical conclusions by distinguishing between descriptive and inferential studies and population and sample statistics.
Measuring and modelling relationships between variables to set-up and run hypothesis tests and correlation and regression analysis.
4.2.1 | Classes of Distributions |
4.2.2 | Inferential Statistics |
4.2.3 | Understanding Inference |
4.2.4 | Sampling techniques & uses |
4.2.5 | Central Limit Theorem and the principal correlations |
4.2.6 | Data Transformation, Box Cox |
4.4.1 | General Concepts & Goals of Hypothesis Testing |
4.4.2 | Significance; Practical vs. Statistical |
4.4.3 | Risk; Alpha & Beta |
4.4.4 | Hypothesis Testing of Means, Variances and Proportions ( Z- , p- and t-tests) |
4.4.5 | 1 & 2 sample t-tests |
4.4.6 | 1 sample variance |
4.4.7 | Paired-comparison tests |
4.4.8 | Single-factor analysis of variance (ANOVA) |
4.4.9 | Tests of Equal Variances. Including Tests of Equal Variance, Normality Testing and Sample Size calculation, performing tests and interpreting results. |
4.5.1 | Mann-Whitney |
4.5.2 | Kruskal-Wallis |
4.5.3 | Mood’s Median |
4.5.4 | Sample Sign |
4.5.5 | Sample Wilcoxon |
4.5.6 | One and Two Sample Proportion |
4.5.7 | Chi-Squared (Contingency Tables)a. Including Tests of Equal Variance, Normality Testing and Sample Size calculation, performing tests and interpreting results. |
4.6.1 | Simple linear correlation and regression |
4.6.1 | Simple linear correlation and regression |
5.0 IMPROVE
8.5 Hours
Apply divergent thinking by using creativity techniques to identify innovative solutions.
Use various tools and techniques for reducing cycle time, including continuous flow, single-minute exchange of die (SMED), etc.
How to make data driven project decisions Build High Performing Teams for project success How to Manage Resistance to Change
5.2.1 | Pull: Takt Time and Line Balancing, Kanban, Supermarket |
5.2.2 | Flow: Batch Reduction, Parallel Processing, Standard Work & Multi skilling, Modular Design, Layout & Cells, Quick Changeover (SMED), Level Scheduling |
5.2.3 | Steps to Perfection, Operational Equipment Effectiveness (OEE), Bottlenecks, Total Productive/Preventative Maintenance (TPM) |
5.2.4 | Assumption Busting the status quo |
6.0 CONTROL
9.5 Hours
Application of Six Sigma Design for Six Sigma (DFSS) Methodology to drive growth through innovation. Application of statistical process control (SPC) including control chart selection for monitoring and controlling process performance, tracking trends, runs and identifying special and common causes using rules for determining statistical control. Develop a Control Plan to emmbed Process Management principles
6.4.1 | Objectives and benefits |
6.4.2 | Rational subgrouping |
6.5.1 | −R, |
6.5.2 | −s, individuals and moving range (ImR / XmR), median |
6.5.3 | p, np, c, and u chart |
6.5.4 | Analysis of control charts |
Quizzes Segmented and embedded during and at the end of each DMAIC Phase
5 hours
Final Exam Lean Six Sigma Black Belt Certification
1 hours
Total Estimated Time to Complete Black Belt Training & Certification:
58 hours
E-Learning Modules
58 Hours
Instructor-led Live Virtual Sessions
18 Hours
Action Learning Project (ALP)
30 Hours
ALP Tollgate Review
6 Hours
Estimated time to complete
Course Duration
112 Hours
15 Weeks
Customize your team training experience
Choice of delivery format (E-Learning, Virtual, Face-to-Face or a mix of all three).
Delivered when, where, and how you want it.
Full-scale programme development.
Tailored content.
Expert team coaching.
A dedicated online learning environment for your organization.
Progress tracking towards project completion and certification.
Click here for more quotes like these.
Ongoing personal and professional development. Recognition and career advancement opportunities.
Part of a strong international network. Join a community of continuous improvement professionals that will support you during and long after the course is over
The quickest, easiest and most engaging way to get individuals and companies on track with Lean Six Sigma concepts and tools.
In-person and virtual workshops
Ready-to-use job aids, tools and templates
Peer-to-peer learning forums
Distinctive digital learning content
Expert coaching support
Nudges, reminders and micro learning
Excellent for remote teams
Auto-translate curriculum and instruction
Multi-channel; eLearning, virtual, face-to-face or in-house
Make progress in less time and deliver results quickly
Tailored learning solutions for companies
Mobile friendly
Highly practical
Join our Lean Six Sigma community
Practice exams
World Class Lean Six Sigma Certification