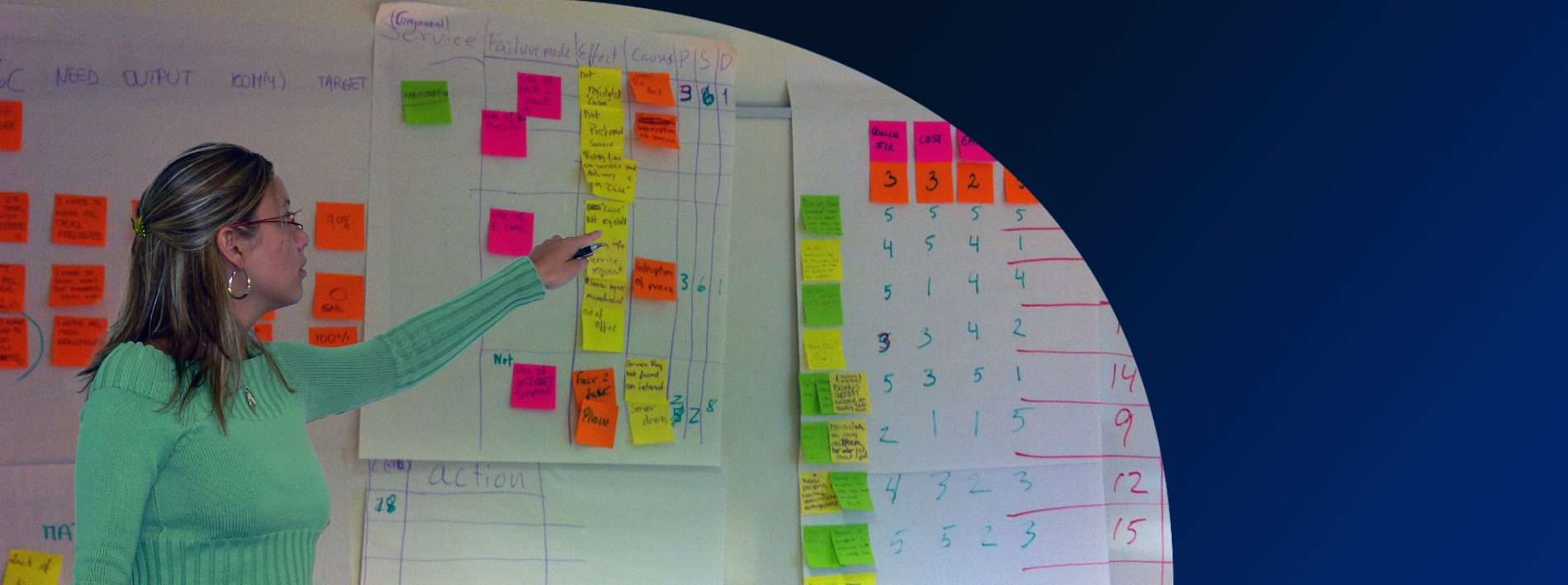
Lean Six Sigma Green Belt Training and Certification will take you on a hands-on learning journey that will help you develop the skills you need to create and implement actionable plans that can help your organization serve customers effectively and efficiently.
The course sets out with an understanding of the fundamental principles of the Lean and Six Sigma, tools and techniques and the Define-Measure-Analyze-Improve-Control (DMAIC) process improvement roadmap. It focuses on how to collaborate to identify process waste, solve problems, manage change and implement significant and sustainable results.
By elevating your problem solving and analytical skills, you will return to work, able to develop and support a continuous improvement culture within your organization. A culture that is capable of confidently creating and sustaining innovative efforts.
How you benefit:
- Learn how to lead process improvement projects using Lean Six Sigma principles and toolkit using the Define-Measure-Analyze-Improve-Control (DMAIC) methodology
- Equipped to deliver customer satisfaction, business efficiency, on time and on quality productivity improvements in any organizational context
- Roadmaps for performance-oriented results: Access resources for creating vision and setting direction to guide individuals, teams and organizations to create a continuous improvement culture that is capable of confidently creating and sustaining improvement efforts
- Facilitate good decision making through the use of statistical data driven tools and techniques
- Acquire the mindset and skills to collaborate with others to identify waste, solve problems, manage change and implement significant and sustainable process improvements
- Return to work able to develop and support a continuous improvement culture within your organization.
Participant profile:
Green Belt Training and Certification is designed for team members, supervisors, project manager’s, functional and technical experts, consultants, senior executives from a wide variety of manufacturing, service and transactional organizations;
- Seeking to learn new problem solving approaches to develop and integrate cutting-edge best practices into their business processes and organizational culture.
- Participants coming in groups/teams to collaborate on Action Learning Project tailored to their organization’s context.
Course Pre-requisites
Interest in developing practitioner level continuous improvement skills
Exam and Certification
Online Exam: 30 questions
Duration: 40 min.
Pass mark: 70%
Achieve 70% pass mark in the Green Belt multiple choice final exam
Participants commit to a series of 8 hour days of intense face-to-face Accelerated learning. The training is practical, precise with no corners cut. Don’t expect an easy ride, you are there to learn and learn you will. We offer action-oriented, interactive courses, packed with examples, case studies and compelling best practices as part of the learning experience. Each course is designed to give participants the level of knowledge, skills and attitude to make a real difference at their workplace.
Our typical training class includes a mix of international participants from a wide variety of industries who bring their experiences to the classroom for in-depth and stimulating learning sessions with fellow participants and instructor’s, so you will take a collaborative approach to the subject matter.
Many of today’s leading organizations and educational institutions are benefiting from the power of Accelerated Learning. Game Change has pioneered and delivered this teaching and learning method for Lean Six Sigma face-to-face training. What makes Accelerated Learning so effective is that it’s based on the way we all naturally learn.
People learn best in context. Facts and skills learned in isolation are hard to absorb and quick to evaporate. The best learning comes from doing the work itself in a continual process of “real-world” immersion, feedback, reflection, evaluation and re-immersion.
Gain insight from world-class Master Black Belt Instructor’s and points of view from people who have faced the real world scenarios in managing the change resistance and barriers to implementation. Expert’s who practice what they preach and believe in their ability to demonstrate the “How” as well as the “What” to do, including compelling best practices and benchmarking opportunities as part of the learning experience.
Case studies and group tutorials conducted during the classroom sessions are designed to ensure you gain a practical understanding of systematically selecting and applying appropriate methods and tools.
The learning outcomes are individually assessed through the final exam on the on the last day of the course.
Curriculum and Course Format
Next Course Dates
E-Learning Modules
6 Hours
Face-to-Face Classroom Training 5 Day x 8 Hours
40 Hours
United Kingdom
7th – 11th Apr 2025
Portugal
This blended course in run jointly with Instituto Superior Técnico and Erising.
Get in touch for next course dates
Classroom training sessions take place in-person between 09:00 to 17:00 BST / 08.00 to 16:00 UTC
Estimated time to complete
46 Hours
Course Fee (excluding VAT)
£ 2,395
What's Included
- 5 days classroom training
- Lunch and refreshments for course duration
- Printed course notes
- 12 month access to eLearning Green Belt course
- 12 month free access to Green Belt Bootcamp Learning Platform, Toolkit, Case Studies and Downloadable Resources
- Green Belt Online Exam and Electronic Certificate
- Unlimited Practice Exams and Re-sits free of charge
- Email Tutor support via discussion groups
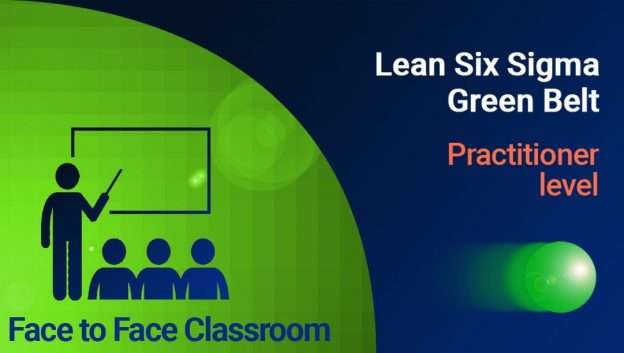
