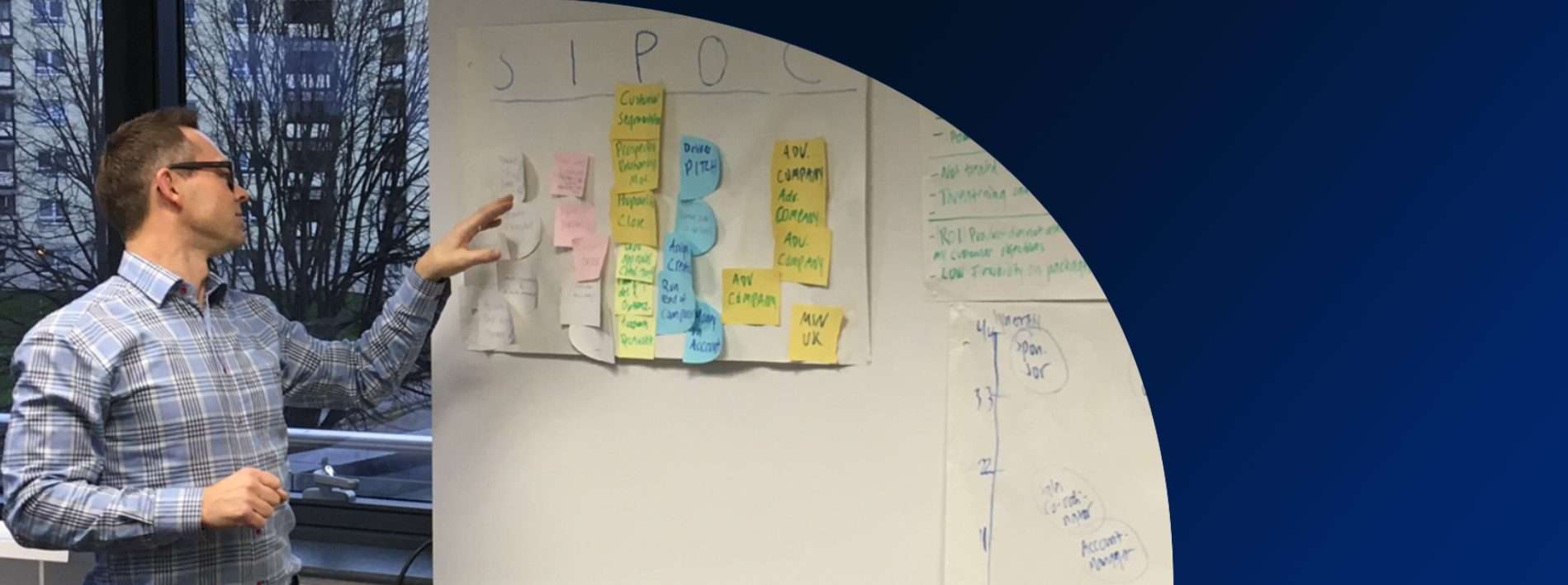
Lean Six Sigma Black Belt Training and Certification equips you with “Advanced Practitioner Level” perspectives and skills in process variability reduction (DMAIC), process waste reduction (LEAN) and a comprehensive toolkit to plan and lead change in your organization.
This course builds upon your Green Belt knowledge to expand your Lean Six Sigma expertise, strengthen your knowledge and skill sets, and gives you the confidence you need to take that next step as a continuous improvement professional and return back to your organization with a greater level of analytical, project implementation and change leadership skills.
You walk away with the learning and the know-how. This means not just focus on the “what” to do but the “how” to do it, with greater emphasis on typical project barriers and “hints” and “tips” on “how” to overcome using case studies and compelling best practices as part of the learning experience.
Participants have the option to complete an Action Learning Project for their organization during the course to help develop a practical understanding of the tools and techniques learned and the ability to understand the big picture and manage the needs of different stakeholders.
How you benefit:
• Sustain actionable knowledge. Harness information you already have into a solid understanding of how to build sustainable processes and structures to enhance your organization’s capability.
• More competent as a manager. Become a more competent and confident manager with new insights, knowledge and skills.
• Elevate key skills in change leadership, analyzing data and decision making to take on greater responsibility to pinpoint and manage performance shortfalls
• Insights on where to focus attention to influence change in your organization and how to identify, scope and charter continuous improvement projects
• Master the skills you need to combine statistical and quantitative methods with the interpersonal skills required to influence, inform and drive change
• Develop coaching skills to guide team members and advise management during Lean Six Sigma implementation.
• Action Learning Project (optional) to apply the learning in your personal or your organization’s context
Participant profile:
Black Belt Training and Certification is designed for Certified Green Belt’s from a wide variety of manufacturing, service and transactional organizations either currently involved with, or who aspire to, or have recently gained continuous improvement responsibilities;
- Seeking to develop in-depth knowledge and analytical skills in process variability reduction (DMAIC) and process waste reduction (Lean)
- Who want to strengthen their ability to lead change and enhance their organization’s continuous improvement capability
- Participants coming in groups/teams to collaborate on an Action Learning project tailored to their organization’s context.
Course Pre-requisites
Green Belt Certification
Exam and Certification
Exam: 50 Questions
Duration: 70 min.
Pass Mark: 70%
Achieve 70% pass mark in the Yellow Belt multiple choice final exam
Participants commit to a series of 8 hour days of intense face-to-face Accelerated learning. The training is practical, precise with no corners cut. Don’t expect an easy ride, you are there to learn and learn you will. We offer action-oriented, interactive courses, packed with examples, case studies and compelling best practices as part of the learning experience. Each course is designed to give participants the level of knowledge, skills and attitude to make a real difference at their workplace.
Our typical training class includes a mix of international participants from a wide variety of industries who bring their experiences to the classroom for in-depth and stimulating learning sessions with fellow participants and instructor’s, so you will take a collaborative approach to the subject matter.
Many of today’s leading organizations and educational institutions are benefiting from the power of Accelerated Learning. Game Change has pioneered and delivered this teaching and learning method for Lean Six Sigma face-to-face training. What makes Accelerated Learning so effective is that it’s based on the way we all naturally learn.
People learn best in context. Facts and skills learned in isolation are hard to absorb and quick to evaporate. The best learning comes from doing the work itself in a continual process of “real-world” immersion, feedback, reflection, evaluation and re-immersion.
Gain insight from world-class Master Black Belt Instructor’s and points of view from people who have faced the real world scenarios in managing the change resistance and barriers to implementation. Expert’s who practice what they preach and believe in their ability to demonstrate the “How” as well as the “What” to do, including compelling best practices and benchmarking opportunities as part of the learning experience.
Case studies and group tutorials conducted during the classroom sessions are designed to ensure you gain a practical understanding of systematically selecting and applying appropriate methods and tools.
The learning outcomes are individually assessed through the final exam on the on the last day of the course.
Our platform provides a single source for all materials and communications related to your studies, making it quick and easy to manage your learning. It has many features which provide a world-class learning experience:
- Course and module updates through our activity feed, which highlight important news, events, and current affairs related to your modules
- An intuitive user interface to keep track of your progress and important deadlines
- 24/7 access to all programme materials, on any device
- Notifications to ensure you don’t miss any critical updates
- Collaborative exercises to build an online community
- Messaging tools and discussion boards to connect you with your peers and tutors
- An interactive video player with transcripts and speed controls
Curriculum and Course Format
Next Course Dates
E-Learning Modules
14 Hours
Face-to-Face Classroom Training 5 Day x 8 Hours
40 Hours
United Kingdom
28th Apr – 2nd May 2025
Portugal
This blended course is run jointly with Instituto Superior Técnico and Erising.
Session 1
(2 Day Face-to-Face or Remote) – 6th and 7th May 2025
Daily Timing: 09:00 – 17:00
Venue: Instituto Superior TécnicoSession 2 (Remote) – Thu 15th May
Session 3 (Remote) – Thu 22nd May
Session 4 (Remote) – Thu 29th May
All remote sessions timing 08:30 – 14:30 Hrs. (6 hrs per session)
Classroom training sessions take place in-person between 09:00 to 17:00 BST / 08.00 to 16:00 UTC
Estimated time to complete
54 Hours
Course Duration
5 Days
Course Fee (excluding VAT)
£ 2,695
What's Included
- 5 days classroom training
- Lunch and refreshments for the course duration
- Printed and eLearning course modules (12 month access)
- 12 month free access to Black Belt Bootcamp Learning Platform, Toolkit, Case Studies and Downloadable Resources
- Black Belt Online Exam and Electronic Certificate
- Unlimited Practice Exams and Re-sits free of charge
- Email Tutor support via discussion groups
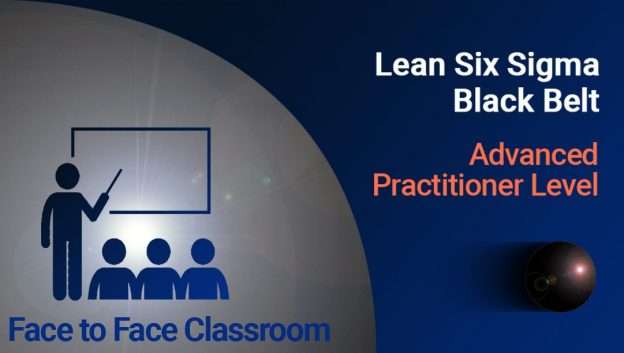
