What is Lean and The Origin of Lean
Taiichi Ohno, who is considered to be the father of the Toyota Production System, once said:
” All we are doing is looking at the time line, from the moment the customer gives us an order to the point when we collect the cash. And we are reducing the time line by reducing the non-value adding wastes”
Since its establishment in 1937, Toyota has developed the improvement system, the ”Toyota Production System”.
This was the system that inspired researchers at the end of the 1980s to define what we know today as the Lean philosophy.
In brief, Lean is meant to simplify operations, eliminate waste, and to carry out more value-creating activities by developing people and processes.
Toyota is nowadays known worldwide for its culture and improvement culture, referred to as the “Toyota Production System”. It is often referred to as the “by the book” way of operating in the ”lean” way. Books normally get outdated as new knowledge is discovered. The Toyota Production System never gets outdated, as it is an integral part of its nature to evolve over time. – The continuous striving for perfection and new levels of performance.
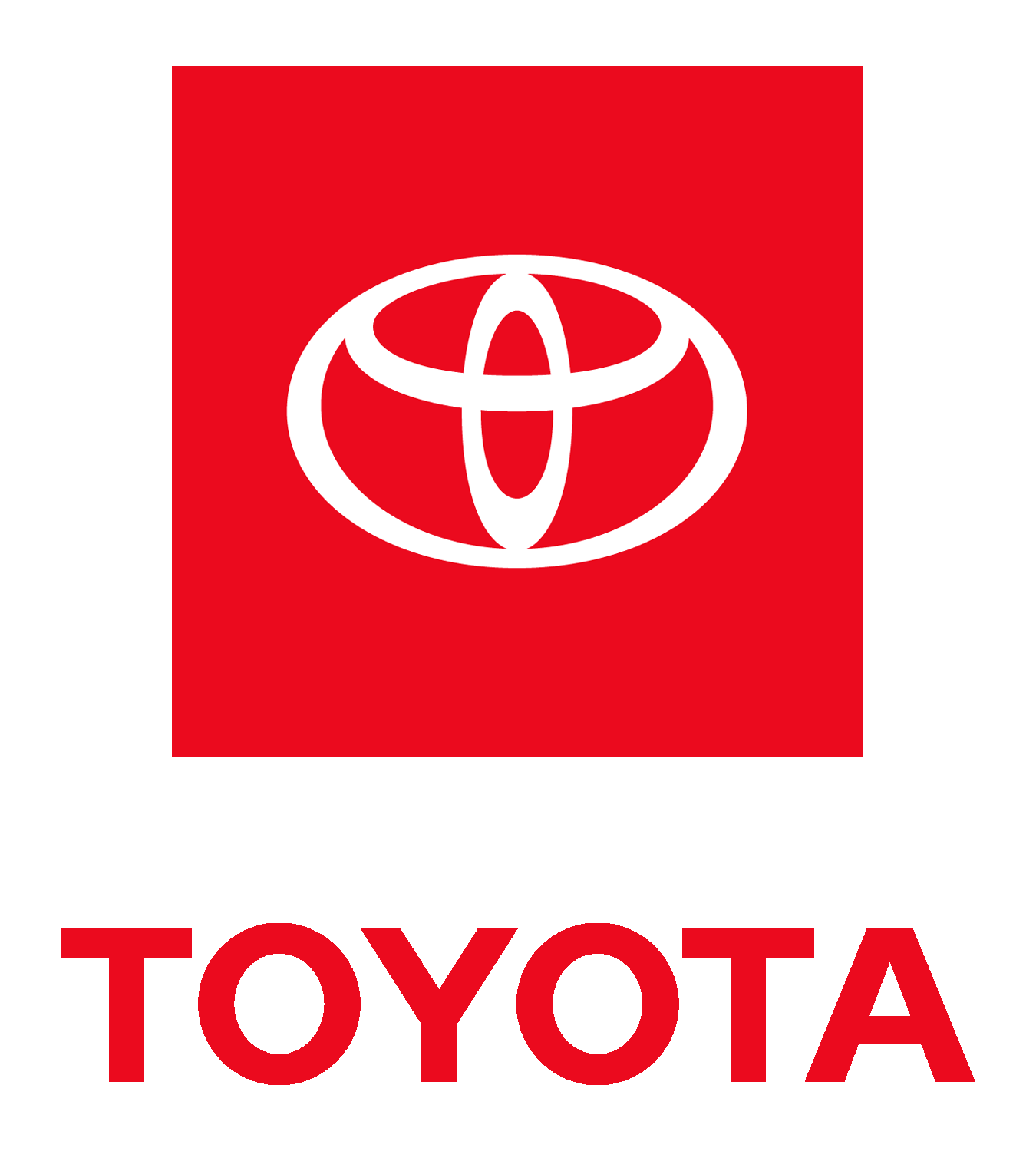
The concept of Lean, quite simply originated in the major study published in 1990 in which production formats, operational philosophies, efficiency, etc. were characterized as being carried out in a streamlined way – “the production is so lean”, was referred to by one of the participants – and the lean concept term was coined.
Without mentioning tools, we can tell you that the philosophy may be explained as follows:
A triangle having empowerment of people at the center, that is firmly supported on a foundation, built on what we believe in, and with two sides in balance between how we lead and manage — and the tools we make use of.
The fact that empowerment of co-workers stands at the center illustrates how far we have moved from the traditional view of ”people as a variable cost”.
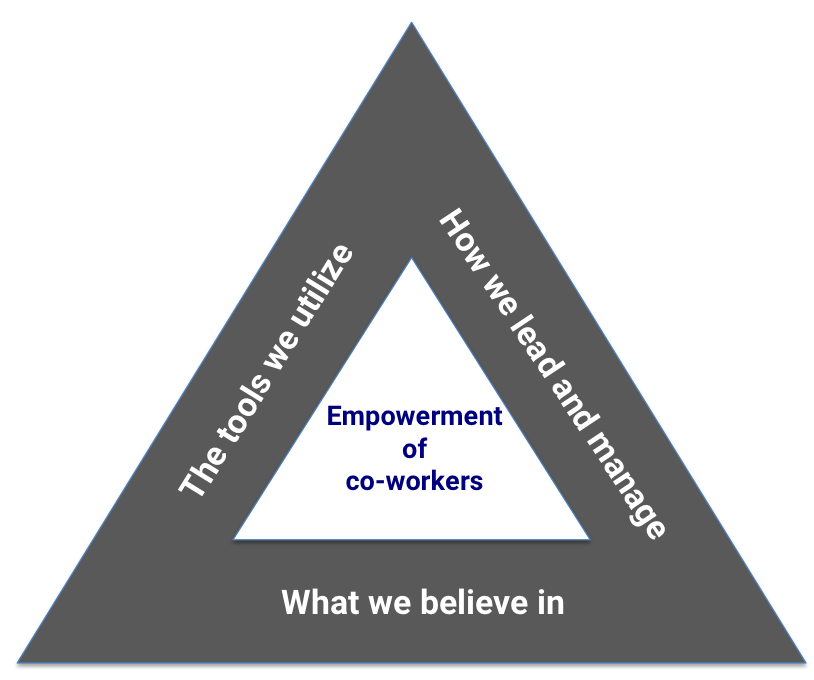
Lean is propelled by a genuine belief that the people within an organization form the most important element, and that these people are the driving force behind any improvement.
The foundation for the triangle is, “what we believe in”. This comprises policies, code of conduct, principles of behavior, and the like. These elements must be lived every day and by each and every one — they cannot be mere fluff.
The right arm of the triangle represents how we lead and manage. In a company working on transforming to ”lean”, major changes away from a traditional leadership style are often required. Traditionally managers expressed a ”You shall” way of addressing their employees. In a Lean organization, we would rather say, ”How do you feel about it?” and “How can I help you solve the problems that exist?”
If we were to summarize the “Lean style of leadership” in three bullet points, they would be:
• Go see (observe and understand)
• Ask why (rather than telling what is right and wrong)
• Show respect (to release the creative power in people)
The left arm of the triangle is what you do — or the tools we utilize.
It is a common misunderstanding to expect Lean to happen by listing one or more tools that are used or that one plans to use. This is a naïve approach. Lean is not a collection of tools, but an integrated philosophy aimed at delivering flawless products and services through producing value for the customer and making them as efficiently as possible. And in this way, we must strive for perfection and balance throughout the triangle.